1. Nitrogen pipeline construction should follow the specifications
"Specification for industrial metal pipeline engineering and acceptance"
"Oxygen station design specification"
"Regulations on safety management and supervision of pressure pipelines"
"Specification for degreasing engineering and acceptance"
"Specification for construction and acceptance of welding engineering of field equipment and industrial pipelines"
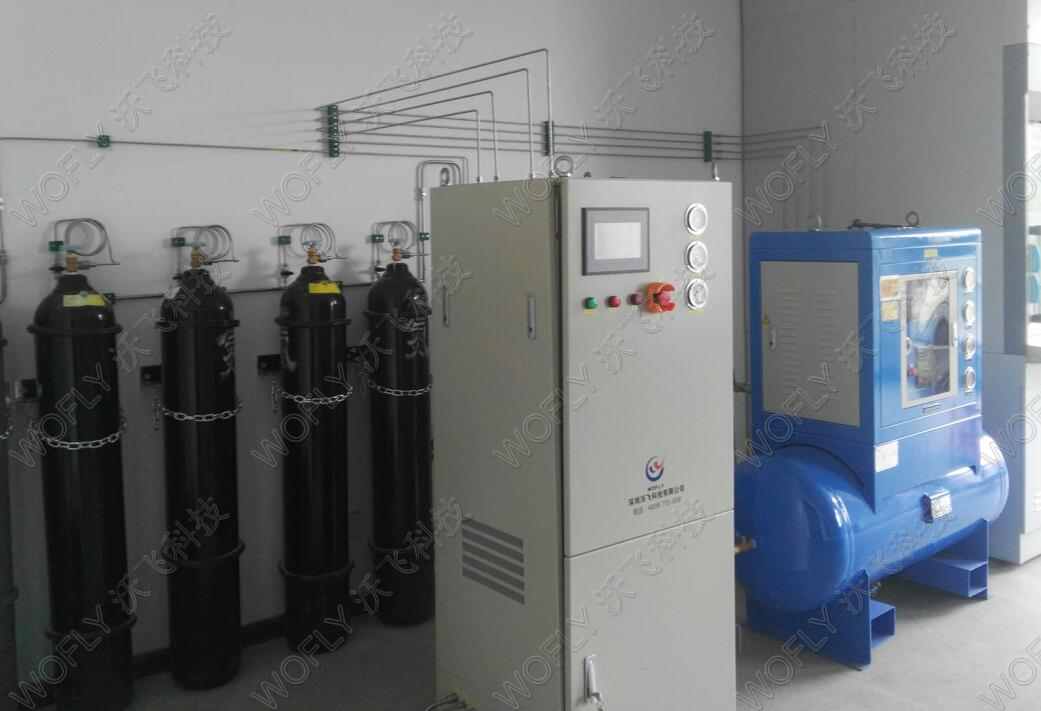
2. Pipeline and accessories requirements
2.1 All pipes, pipe fittings, and valves must have ex-factory certificates. Otherwise, check the missing items and their indicators should meet the current national or ministerial standards.
2. 2 All pipelines and accessories should be visually inspected, such as whether there are defects such as cracks, shrinkage holes, slag inclusions and heavy leather to ensure that the surface is smooth and clean; for the valves, strength and tightness tests should be carried out one by one (the test pressure is the nominal pressure 1.5 The pressure holding time is not less than 5 minutes); the safety valve should be debugged more than 3 times according to the design regulations.
3. Pipe welding
3.1 In addition to meeting the requirements of the drawings, the welding technical conditions should be carried out in accordance with international regulations.
3.2 The welds should be inspected by radiographic or ultrasonic in accordance with the specified quantity and quality level.
3.3 Welded carbon steel pipes should be backed with argon arc.
4. Pipeline degreasing and rust removal
Use sandblasting and pickling to remove rust and degrease the inner wall of the pipeline.
5. Precautions for pipe installation
5.1 When the pipeline is connected, it must not be forcefully matched.
5.2 Check the straightness of the butt connector of the nozzle. Measure port at a distance of 200mm. The allowable deviation is 1mm/m, the total length deviation is less than 10mm, and the connection between the flanges should be parallel.
5.3. Use threaded connectors to apply PTFE with packing, and it is forbidden to use sesame oil.
5.4. The pipe and the support should be separated by a non-chloride ion plastic sheet; the pipe through the wall should be sleeved, and the length of the sleeve should not be less than the wall thickness, and the gap should be filled with non-combustible materials.
5.5. The nitrogen pipeline should have lightning protection and electrostatic discharge grounding devices.
5.6. The depth of buried pipeline is not less than 0.7m (the top of the pipeline is above the ground), and the buried pipeline should be treated with anticorrosion.
6. Pipeline pressure test and purge
After the pipeline is installed, conduct a strength and tightness test, and the regulations are as follows:
Working pressure | Strength Test | Leak Test | ||
MPa | ||||
Media | Pressure(MPa) | Media | pressure(MPa) | |
<0.1 | Air | 0.1 | Air or N2 | 1 |
≤3 | air | 1.15 | Air or N2 | 1 |
water | 1.25 | |||
≤10 | water | 1.25 | Air or N2 | 1 |
15 | water | 1.15 | Air or N2 | 1 |
Note:
①Air and nitrogen should be dry and oil-free;
②Oil-free clean water, the chloride ion content of the water does not exceed 2.5g/m3;
③All intensity pressure tests should be carried out slowly step by step. When it rises to 5%, it should be checked. If there is no leakage or abnormal phenomenon, the pressure should be increased step by step at 10% pressure, and the voltage stabilization for each step should not be less than 3 minutes. After reaching the pressure, it should be maintained for 5 minutes, and it is qualified when there is no deformation.
④ The tightness test will last for 24 hours after reaching the pressure, and the average hourly leakage rate for indoor and trench pipelines should be ≤0.5% as qualified.
⑤After passing the tightness test, use oil-free dry air or nitrogen to purge, with a flow rate of not less than 20m/s, until there is no rust, welding slag and other debris in the pipeline.
7. Pipeline painting and work before production:
7.1. The rust, welding slag, burr and other impurities on the painted surface should be removed before painting.
7.2. Replace with nitrogen before putting into production until the purity is qualified.
Post time: Jun-25-2021