Shenzhen Wofly Technology Co., Ltd. specializes in the research and development and manufacture of high-clean centralized gas supply systems and fluid control related parts, components, system equipment, valves, pipe fittings, instruments, etc., and is also Atlas Copco's national general agent. Products are mainly used in semiconductor, gas, chemical, biotechnology, nuclear power, aerospace, food and other industries. The company is equipped with several Swagelok's most advanced high-tech pipeline automatic welding equipment, providing overall solutions for fluid systems, and is a collection of product sales channels. It is a comprehensive company integrating system design, installation and construction.
Design and construction, and provide various safety protection systems, among which the laboratory gas pipeline system includes the laboratory centralized gas supply system and the indoor gas cylinder gas supply system, which can meet your different levels of gas safety requirements.
The central gas supply pipeline system project is mainly to provide standard gas with stable value and pressure for the analysis equipment selected by the test/laboratory to ensure the safety of its storage and use. Ensure that the analysis and testing personnel are protected from toxic and harmful gases in the experiment. According to the requirements of the national standard, all the gases used are stored in the gas storage room, and centralized transportation is realized to form a central gas supply system. The system adopts one-to-one, one-to-many, multi-to-many and multi-to-many pipeline gas transmission modes, which can realize segmented control when one tow and many times, and can realize switching control when multi-tow and many times; and can guarantee The standard gas flow rate, pressure stability and quantity value transmission do not change, which meets the technical requirements of analysis and testing equipment for the gas used.
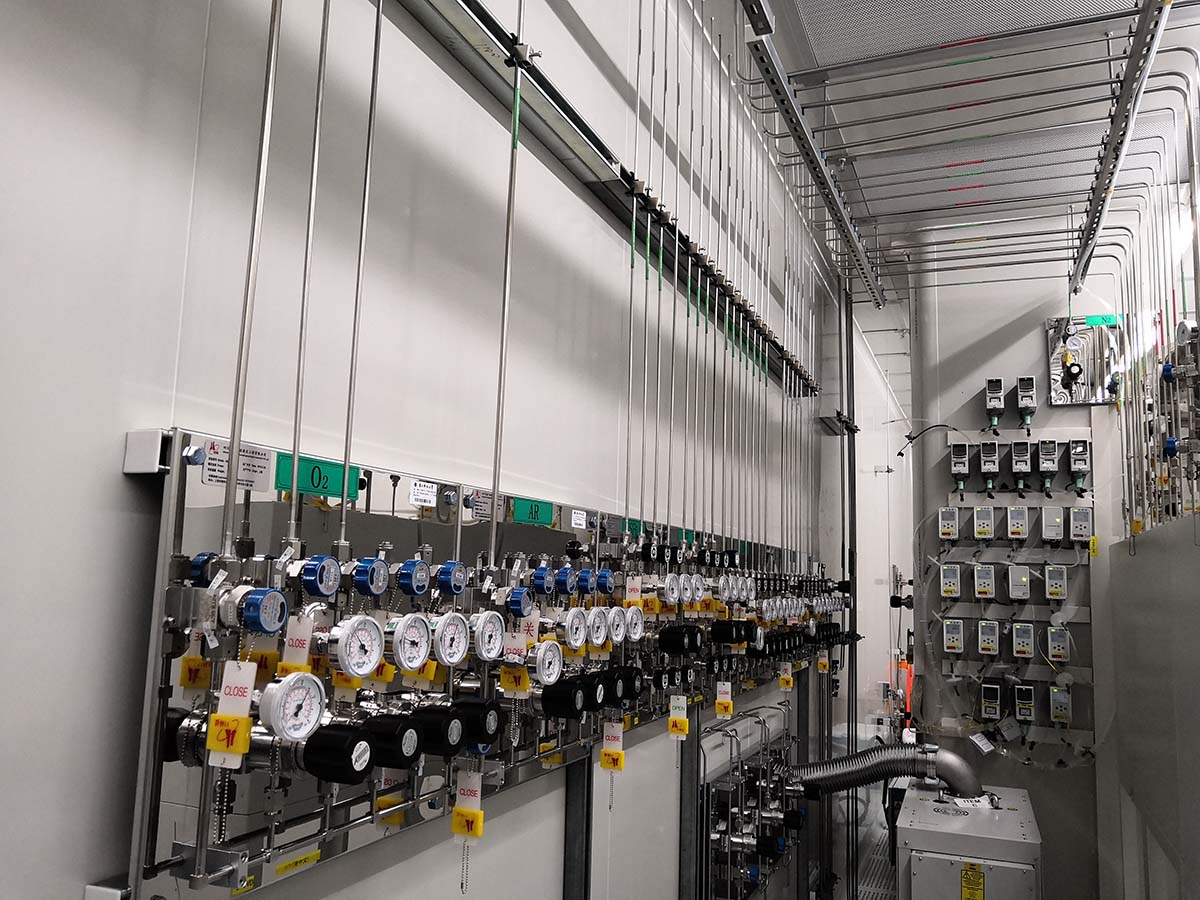
This part introduces the design, material, transportation, installation, inspection and other aspects of the gas pipeline. The gas pipeline is installed from the main valve of the gas cylinder station to the various gas valves on the workbench. There are 6 kinds of gases used in the CCIQ laboratory. The main gases include: argon, helium, oxygen, compressed air, acetylene, and nitrous oxide. It can be put into storage after confirmation.
The laboratory gas cylinder area is introduced by pipeline. Except for instrument air (factory air), which is directly produced by the factory, all other gases are supplied by high-pressure gas cylinder cabinets. Install semi-automatic switching valves to control the replacement of gas cylinders. The main control valves and pressure reducing valves are installed outside the laboratory. The main material of the laboratory gas pipeline is stainless steel. It is recommended to install it under the ceiling and walk along the wall to facilitate inspection and maintenance (it can also be determined according to the customer and site conditions).
In addition, the gas pipeline of the central station is introduced through the service column. All gas pipelines are equipped with appropriate control valves on the workbench for easy operation. All gas pipeline connections are seamlessly welded. The compressed air introduced into the general analysis laboratory needs at least 2 compressed air cylinders to back up. The gas pipeline is made of stainless steel, and there is a purification device on the pipeline to filter out impurities and moisture. This purification device is connected in parallel with a pipeline and isolated by a separate valve, so that the filter device can be repaired without affecting the normal use.
There is a semi-automatic regulating valve between the used gas cylinder and the spare gas cylinder to control. All gas lines are of high quality, fully annealed, seamless stainless steel SS-316L. All gas pipelines must be completely cleaned to make them suitable for gas use. The gas pipeline needs to have a safety pressure release valve, a pressure regulating valve, and a pressure gauge to indicate the gas pressure.
All pressure reducing valves need to be connected to an exhaust line leading out of the gas storage area. Flammable and oxidizing gas exhaust pipes cannot be combined together. The coil is made of stainless steel, which has sufficient toughness. The safety relief valve must be marked to indicate the pressure release level. All valves, regulating devices, and pressure gauges are made of high-quality stainless steel. And they are all standard accessories.
Fittings and valves generally use AFK, swagelok, APtech or similar brand products. Provide gas back to the controller. All pipelines are marked with connected gas. All pipelines can be used normally under the environment. Preparation of the construction site: The construction site should reach three links (road, electricity, and water) and one level (site leveling) before construction. Materials and construction equipment should be stacked according to the construction plan, and the prefabricated pipelines and temporary facilities should be reasonably arranged.
The flammable (flash point lower than or equal to 45℃) items within 30m beyond the construction boundary line have been cleared or measures have been taken to prevent open flames. The route and construction plan for buried pipeline and pipe jacking construction have been confirmed and approved by relevant units, and protective measures have been taken. The construction monitoring area has been clearly marked. The temporary scaffolding required for pipeline construction and the support in the trench have been erected as required and passed the inspection.
Laboratory gas pipeline engineering materials and construction equipment preparation:
1. Piping components (pipes, valves, pipe fittings, flanges, compensators, gaskets, fasteners, expansion joints, flexible joints, pressure joints, pressure hoses, steam traps, filters, separators Etc.), pipe supports include installation parts (hanger rods, spring hangers, diagonal rods, counterweights, elastic bolts, support rods, chains, guide rails and anchors, as well as load-type fixing parts, such as saddles, bases, rollers, Brackets and sliding supports) and attachments (pipe hangers, lugs, snap rings, pipe clamps, U-shaped clamps, fastening splints and skirt pipe sockets), as well as pipe welding materials (welding rods, welding wires, flux, protection Gas), etc. should be supplied according to the pipeline system and according to the requirements of the construction period to meet the construction schedule. Other materials such as glass fiber reinforced plastic, rubber, plastic, paint, heat insulation (heat or cold insulation) materials, waterproof materials, anti-corrosion materials, etc., can be guaranteed to be supplied according to the requirements of the construction period.
2. The arrival inspection and testing of the pipeline components have been basically completed, and marked according to the specified requirements, and the conditions for commissioning are met. The remaining inspection and testing work can meet the requirements of the construction period according to the inspection and test plan. The construction equipment has been configured according to the resource allocation plan. Inspection and testing equipment, non-destructive testing equipment, measuring instruments, etc. should meet the requirements of pipeline construction inspection and testing, and be qualified and within the validity period.
The storage of piping components should meet the following requirements: storage according to types, materials, specifications, and batches; stainless steel, carbon steel, and low-alloy steel piping components must not be in contact; piping components stored outdoors should be provided with supports and cushions; The materials stored on the construction site should be neatly placed, clearly marked, and dedicated to special materials. When piping components are issued, the material, specification, model, quantity and identification shall be checked. The logo should be transplanted before the material is cut.
The appearance quality of steel pipes used in laboratory gas pipeline engineering should meet the following requirements: There should be no cracks, folds, rolls, separations and scars on the inner and outer surfaces of the stainless steel seamless steel pipes. On the inner and outer surfaces of the steel pipe, the allowable depth of the straight line is as follows: cold drawn (rolled) steel pipe: no more than 4% of the nominal wall thickness and no more than 0.30mm; hot rolled (extruded) steel pipe: no more than 5% of the nominal wall thickness, diameter For steel pipes less than or equal to 140mm, the maximum allowable depth is 0.5m; for steel pipes with a diameter greater than 140mm, the maximum allowable depth is 0.8mm; the inner and outer surfaces of stainless steel welded steel pipes should be smooth, and there should be no cracks, folds, delamination, pickling and scale. . Minor scratches, pits, and pits with a depth that does not exceed the negative deviation are allowed. The height of the weld ribs shall not be greater than 15% of the wall thickness, and the minimum height is 0.18mm.
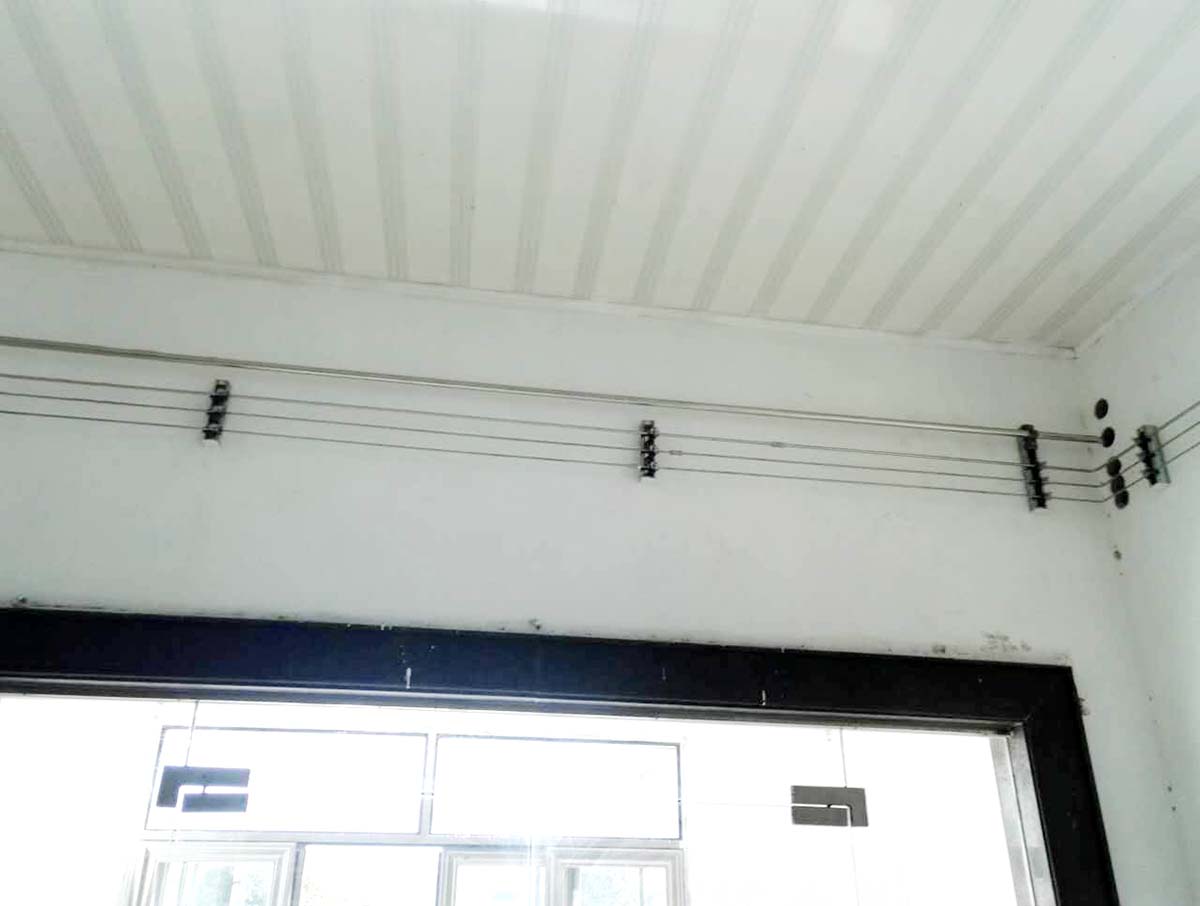
The inner and outer surfaces of seamless steel pipes of other materials are not allowed to have cracks, folds, folds, scars and delamination, and these defects must be completely removed. The removal depth shall not exceed the negative deviation of the nominal wall thickness. The actual wall thickness at the removal site is not less than the minimum allowable wall thickness, but other defects that do not exceed the negative deviation of the wall thickness are allowed; the inner and outer surfaces of the welded steel pipes of other materials should be smooth, and no folds, cracks, and delamination are allowed. There are lap welding defects. The surface of the steel pipe is allowed to have defects such as scratches, scratches, weld dislocation, burns and scars that do not exceed the negative deviation of the wall thickness. Thickening of the wall thickness at the weld and the existence of internal weld ribs are allowed; the inner and outer surfaces of the steel coil tube should be smooth and free of oxide scale, and the weld should be smoothly transitioned. There should be no defects such as cracks, lack of fusion, and lack of penetration, and no molten metal should be left. Slag and spatter.
There shall be no scars, folds, delaminations, or scratches on the body that are greater than 5% of the nominal wall thickness and greater than 0.8mm. There shall be no mechanical scratches and pits with a depth greater than 12% of the nominal wall thickness and greater than 1.6mm. The size of the steel pipe should meet the requirements of SH3405 in the "Steel Pipe Size Series for Petrochemical Enterprises".
General seamless steel pipes made of 10, 20, 09MnV and 16Mn steels suitable for conveying fluids. The allowable deviation of outer diameter and wall thickness shall not exceed the requirements of Table 3.2.6. For steel pipes with requirements for resistance to intergranular corrosion, the results of the intergranular corrosion test should be indicated on the product quality certificate, otherwise, supplements should be made in accordance with the relevant provisions in the "Test Method for the Tendency of Stainless Steel Intergranular Corrosion" GB4334.1-9 Items.
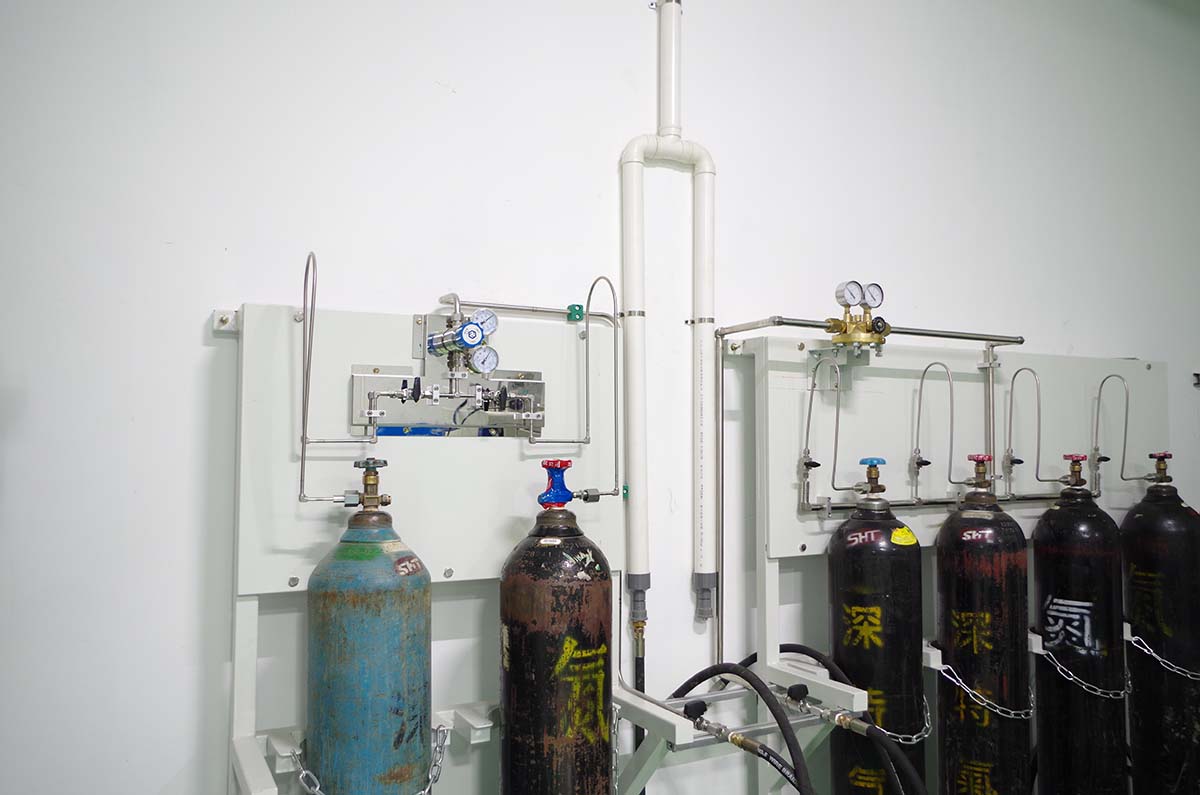
Post time: Jun-18-2021